Services - Product Design Services
About Product Design Services
At Batnon, we specialize in bringing ideas to life through our comprehensive product design services. Our expertise encompasses New Product Development (NPD) and Industrial Design, ensuring that your concepts are transformed into innovative, market-ready products. With a focus on creativity, precision, and functionality, we leverage our “Integrated Process” approach to deliver exceptional results.
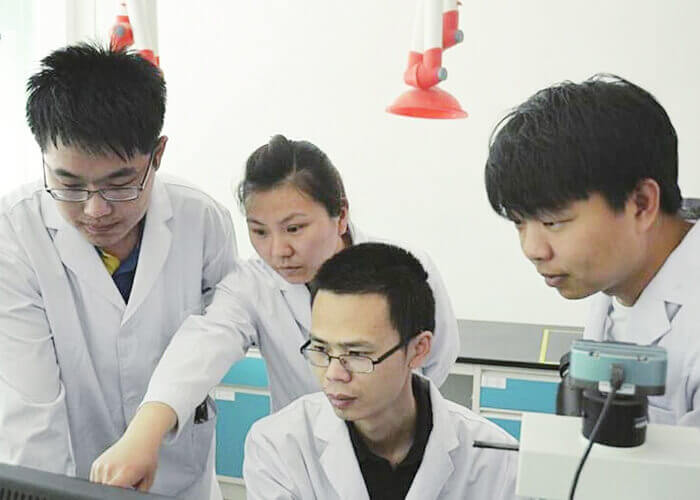
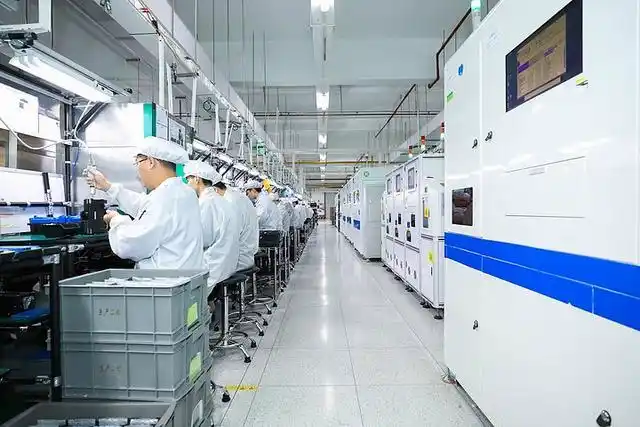
New Product Development
New Product Development (NPD) at Batnon is a structured yet flexible process designed to turn concepts into high-quality products efficiently and cost-effectively. Here’s how we do it:
At Batnon, we specialize in new product development that brings your ideas to life. From initial concept through to prototype and final production, we offer end-to-end support to help you create high-quality, custom products that meet your exact specifications.
Whether you’re launching a new product or improving an existing design, our expert team is here to guide you every step of the way.
1. Conceptualization & Design
Our new product development process begins with a detailed consultation to understand your vision, objectives, and product requirements. During the conceptualization phase, we work closely with you to turn your ideas into a feasible design.
- Collaborative Brainstorming: We engage with your team to understand market needs and consumer demands, ensuring the product meets industry standards.
- Design Prototyping: Using advanced CAD software and simulation tools, our engineers create 3D models and prototypes to visualize the product and test its functionality.
- Design Review & Refinement: We present the design to you for feedback, making iterative adjustments to ensure it meets your expectations.
2. Engineering & Technical Development
Our skilled engineers take your design to the next level by transforming it into a manufacturable product. With decades of experience in precision engineering, we ensure that your product is not only innovative but also feasible, efficient, and cost-effective.
- Material Selection: We advise on the best materials for your product based on durability, functionality, and cost-effectiveness.
- Prototype Development: Our prototyping process involves creating functional prototypes for real-world testing, ensuring performance and design integrity.
- Engineering Analysis: We conduct stress testing, thermal simulations, and other analyses to ensure your product can withstand real-world conditions.
3. Manufacturing & Production
Once the design is finalized, we move to the manufacturing phase. With our comprehensive in-house capabilities in CNC machining, injection molding, die casting, and other production methods, we ensure efficient and high-quality production of your product.
- Precision Manufacturing: Using state-of-the-art equipment, we create prototypes and final products with high precision, ensuring tight tolerances and excellent finish.
- Tooling & Molds: For products requiring injection molding or die casting, we design and create high-quality molds and tooling for efficient mass production.
- Scaling Production: Whether you need small batch runs or large-scale manufacturing, we provide flexible solutions to suit your production requirements.
4. Testing & Quality Control
We place a strong emphasis on quality at every stage of the product development process. Rigorous testing and quality control procedures are in place to ensure your product meets the highest standards before reaching the market.
- Functional Testing: We perform detailed tests to ensure the product performs as expected under different conditions.
- Quality Inspections: From material inspections to final product checks, we use the latest quality control methods, such as CMM and laser measurement systems, to verify product dimensions and overall quality.
- Compliance Testing: We ensure your product meets the necessary regulatory standards and certifications for your target market.
5. Packaging & Final Delivery
Once your product is tested and approved, we take care of the final packaging and delivery. Our efficient logistics ensure that your products reach you on time and in perfect condition.
- Packaging Design: We offer customized packaging solutions that protect the product and enhance its appeal in the market.
- Global Shipping: We provide international shipping, ensuring your products reach your business or customers efficiently and cost-effectively.
- After-Sales Support: Our team is available to provide ongoing support for any further refinements or adjustments after your product is launched.
Industrial Design
Industrial design at Batnon combines aesthetics, functionality, and innovation to create products that stand out in the market. Our design philosophy ensures that every product is visually appealing, user-friendly, and aligned with client goals.
1. Design Principles
User-Centric Approach: Prioritizing user needs, comfort, and accessibility.
Sustainability: Incorporating eco-friendly practices and materials.
Ergonomics: Designing products for optimal usability and interaction.
2. Design Process
Concept Sketching: Creating initial designs and visual representations.
3D Modeling: Using advanced CAD software to develop detailed models.
Design Validation: Testing designs for functionality, aesthetics, and feasibility.
3. Collaboration and Customization
Client Involvement: Working closely with clients to ensure designs align with their vision.
Customization: Offering tailored solutions for unique market demands.
4. Integration with Manufacturing
Prototyping: Ensuring seamless transition from design to production with functional prototypes.
Material Feasibility: Selecting materials that balance design integrity with cost-efficiency.
Production Alignment: Collaborating with manufacturing teams for consistent results.
Why Choose Batnon for Product Design?
1. Comprehensive Expertise
Our team of designers and engineers excels in both creative and technical aspects, ensuring well-rounded solutions.
2. Integrated Process
We combine advanced technologies, skilled labor, and efficient workflows to deliver high-quality designs and products.
3. Client-Centric Approach
We prioritize client goals, ensuring that every design reflects their vision and meets market demands.
4. Cost-Effective Solutions
By streamlining processes and optimizing resources, we deliver premium designs without breaking the budget.
5. Sustainable Innovation
We integrate eco-friendly practices into our design and development processes, contributing to a greener future.
Case Studies
Case Study 1: Consumer Electronics Design
Developed a sleek, user-friendly electronic gadget that achieved market success through innovative features and ergonomic design.
Case Study 2: Industrial Equipment Redesign
Redesigned a complex industrial machine for improved efficiency, safety, and aesthetics, reducing production costs by 25%.
Ready to bring your product idea to life? Contact us today to learn how our New Product Development and Industrial Design services can help you create innovative, market-leading products.